Our Modular Panel System (MPS)
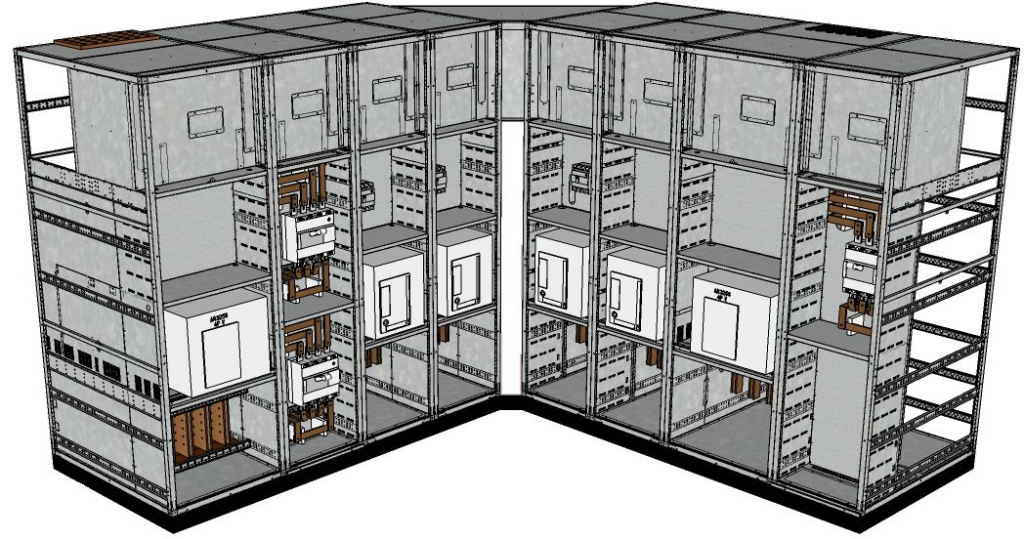
MPS utilises pre-formed components which are fitted together to create an enclosure built to individual client specification, forming an integral part of the final product which is constructed in line with BS EN 61439 Part 2. The use of a standard parts list means the panels can be constructed from “off the shelf” components. This brings about an ease of manufacture that enables panel enclosures to be assembled on the workshop floor days after design approval, rather than weeks, ready for electrical component fitting and wiring.
The speed of installation is further enhanced by the use of plug in technology on the Main Incomers, Feeders, Motor Starters and Moulded Case Circuit Breakers up to 800A rating. These components plug directly onto the Bus Bar system thereby greatly reducing installation, modification and repair time and cost. This feature also makes site alterations and additions to the panel quick and easy as there is no additional drilling or Busbarring required keeping shutdown times and site disturbance to a minimum.
Withdrawable & Fixed Pattern MCCs
Max Wright Ltd offer a variety of automation solutions, ranging from small single pump control panels to large fixed pattern or withdrawable MCCs. Each MCC is custom built to individual client requirements where our experienced engineers are able to offer technical support and design advice throughout the project lifetime. We encourage our customers to engage with us at the earliest stage possible to enable us to work together, engineering out potential unforeseen issues before they become a reality. Whether your requirement is for a small DOL starter panel or a large back to back arrangement MCC with multiple VSD’s, our capable project teams will be able to provide the most economical, technologically advanced and appropriate solution for your needs. All Max Wright Ltd panels are fully type tested, up to 80kA for 1 second or 50kA for 3 second fault rating. Aided by our steelwork division, we are able to manufacture front or rear access, back to back, L or U shaped enclosures, suitable for either top or bottom cable entry. Usually our products operate at 400V, however other Low Voltages such as 690V can also be offered. In conjunction with our Systems Integration and site installation departments, we are able to offer a complete industrial controls solution.
Turnkey Projects & Full Site Installations
With an ever expanding range of skills, Max Wright Ltd are able to provide our clients with full turnkey solutions, providing all services from initial design to manufacture, electrical installation and site management. Using our vast experience in all sectors, we are able to take the strain off of our clients, advising and updating progress as and when required. We are great believers in early client engagement and find this to be a priceless tool when it comes to delivering turnkey projects. At design stage, we will ensure that all critical personnel within the project team are involved to ensure the optimum solution is achieved and subsequently delivered to the customers satisfaction. Adopting this method of working enables both ourselves and our clients to successfully schedule all movements and processes, allowing for a smooth transition between stages, free flowing communication and a flawless end product.
Software & Systems Integration
Max Wright Ltd’s systems and software division work in conjunction with our electrical teams to offer a complete automation solution. Our experienced software engineers undertake all aspects of the project including creation of Functional Design Specifications, PLC coding, creation of HMI graphics and SCADA control systems through to installation and final on site commissioning. With our vast experience across multiple platforms including Mitsubishi, Rockwell and Omron, our engineers are able to tackle complex procedures whilst offering constructive advice to the client giving them strong confidence in the end product. Adding to the flexibility of our culture, we are able to offer separate “bench testing” for panel software enabling optimum lead times. Our customers are always welcome to attend our Hertfordshire workshops for updates on progress and working demonstrations as we progress. The ability to offer this complete service using entirely our own resources, has gained us an enviable reputation within the panel industry and placed Max Wright Ltd in an advantageous position in the competitive market.
Control Panels & Marshalling Boxes
We pride ourselves on the ability to undertake any size project, from the smallest of marshalling boxes, comprising merely a few push buttons, to large Motor Control Centres alongside full electrical installations. Working with our steelwork fabrication division, we are able to produce enclosures of any shape and size, with front or rear access depending on the available space. Our engineers are always more than happy to attend site to investigate the available area, working with our client to establish the best solution. Depending on customer specifications and final position, we are able to construct any panel from either mild or stainless steel, incorporating mimics or annunciators using pneumatic technology if required. Speaking to our engineers and engaging them at the earliest stage possible will allow for us to be able to offer the most cost efficient and application appropriate solution.
Welded Enclosures & Custom Steelwork
Over the past few years, Max Wright Ltd have developed and manufactured a quick and easily constructed “Modular Panel System” (MPS), using pre-formed components fitted together to create a Motor Control Centre, LV Switchboard or Control Panel enclosure. With the use of “Plug In” technology on incoming and outgoing ways at 50mm increments, we are able to provide true flexibility and choice of panel layout, also enabling us to offer unbeatable lead times. Due to the nature of the system and the stock held at our steelwork division, it is possible for our project team to receive a panel order and have the MCC enclosure frame on the shop floor the next day, ready for fitting of components.
The panel design incorporates innovative and unique connecting blocks designed in house. These can be connected anywhere on the framework at 25mm intervals and are used to attach horizontal and vertical profiles and shelves. The connecting block also seals the profiles and shelves to the framework, giving the customer a choice of protection ranging from IP31 to IP54. This system really comes in to its own when there is a need for enclosure modifications at a late stage. Instead of having to re-engineer and potentially re-fabricate an enclosure, potentially adding weeks on to lead times, we are able to simply add columns and shelves to the current design with minimal impact on cost and delivery schedules.
We are also able to offer welded enclosures, custom made to client specification. With our years of experience and modern facilities, Max Wright Ltd always endeavour to help our clients as much as possible in offering solutions and providing unparalleled levels of customer service throughout.
To supplement our range of enclosures, our workshop is fully equipped with modern CNC punching, folding and welding facilities, we can offer product options such as frames, stands and sun shields.
Certified Busbar Systems
Max Wright Ltd manufacture our own busbar systems in house, which are ASTA and KEMA certified with either 25kA for 1 Second, 50kA for 1 second, 50kA for 3 seconds or 80kA for 1 second fault ratings. Individual panel sections are connected to the main busbars by plug-in connectors, enabling speedy installation or removal if required. Both the main through busbars and the dropper bars are installed in a 2mm press formed chamber giving segregation from other panel sections. Standard supports are moulded glass filled nylon and positioned to allow the plug-in connectors at 500mm increments. For specialist applications Max Wright Ltd can manufacture suitable supports in house giving complete freedom of design. Please feel free to contact our experienced engineers to discuss your application and we will be more than happy to help.
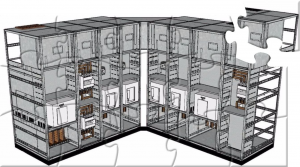
The MPS system provides clients with the opportunity to make design amendments at any stage during the project with minimum impact on the lead time. As an example, the modification of a 600mm high section can be simply turned in to two 300mm high sections simply with the addition of a pre-manufactured shelf and back plates

Our MPS gives the client unrivalled flexibility to carry out modifications post installation. As all holes and installation points are pre-drilled, our site operatives are able to carry out many site modifications with the simple addition or removal of doors, shelves and backplates considerably reducing downtime.
Site Modifications
Our MPS gives the client unrivalled flexibility to carry out modifications post installation. As all holes and installation points are pre-drilled, our site operatives are able to carry out many site modifications with the simple addition or removal of doors, shelves and backplates considerably reducing downtime.
Environment
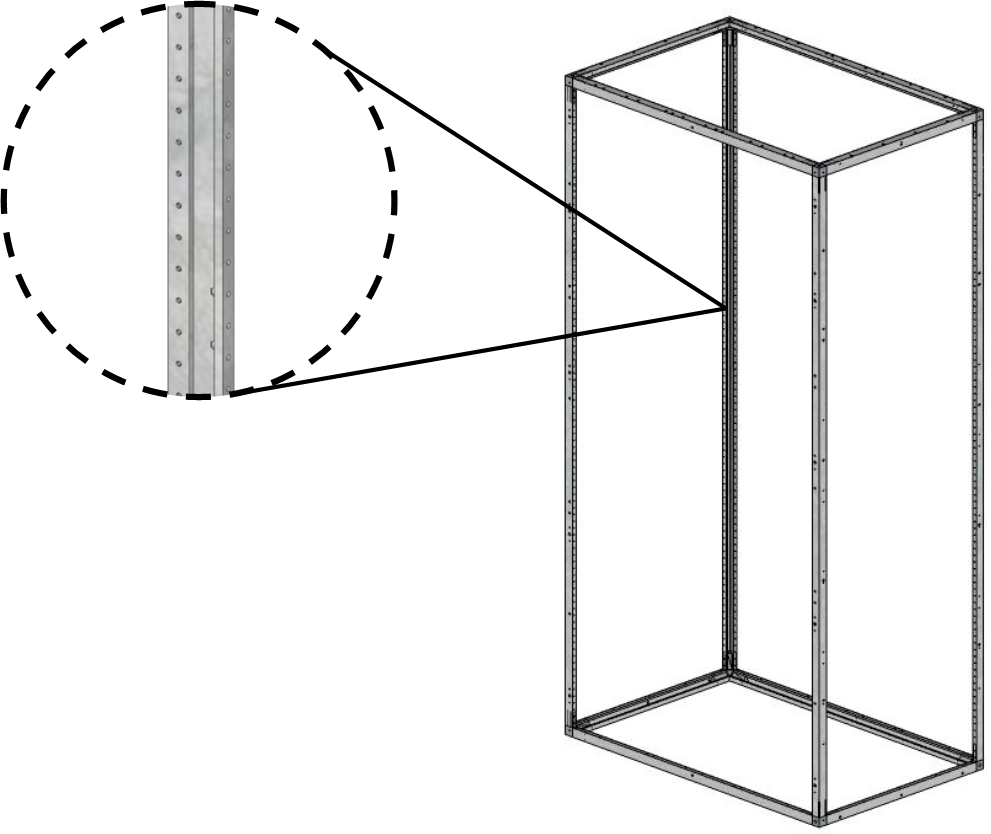
Lead free galvanised structure:
Due to the MPS frame being manufactured using lead free galvanised steel
Only the external doors, covers and plates will need to be sprayed which provides the opportunity for substantial time and cost savings within the project while also significantly reducing environmental impact.